Crawl, Walk, Run, Fly: A Supply Chain Optimization Journey
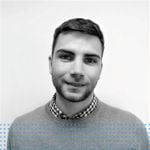
During the past months, the supply chain world has experienced several major disruptions (COVID-19, the Suez Canal blockage, etc.). Agile supply chain planning and fast decision-making have become more important than ever. On the other hand, due to the increasing complexity of value chains, decision-making is becoming more difficult.
What we see amongst our customers is that using spreadsheets and disconnected tools is not suitable anymore to keep up with the complexities of the modern supply chain world, or to assure fast and reliable decision-making to achieve optimized plans.
Anaplan has some key characteristics and functionalities to help fill in the mentioned gap, which currently exists in many organizations, no matter what planning maturity the organization is currently at. Moreover, Anaplan can be a key enabler to bring organizations to the next levels of planning maturity, and thus supporting a true supply chain optimization journey. Let's take a look at how Anaplan provides value at different stages of a supply chain optimization journey.
Crawling (Manual Planning)
In a supply chain optimization journey's first stage, the organization is crawling. They have their own way of working with a lot of custom-made Excels, possibly linked to some legacy planning or ERP system. On the one hand, they are feeling comfortable using them, but on the other hand, there exists a lot of pain points, and they know that there should be a more reliable and better way of working.
However, making the switch to a planning tool can be difficult for many reasons. For many implementations of a planning tool, there is a high dependency on IT. When the process changes, new requirements are identified, or requirements change, the support to change the tool is often not sufficient. Planners will go back to using custom-made Excels outside of the tool. Anaplan is very suited to take the first step away from spreadsheet planning, as the planning tool is business-owned and flexible, and it is using an agile building methodology to keep up with changing requirements.
At this stage, the organization would still be planning manually, but they can build the necessary modules and views to replace the Excels with Anaplan. The DataHub will serve as the single source of truth, and any changes in the model will trigger real-time recalculations through the entire Anaplan model, which is made possible by the HyperBlock.
Walk ( Heuristics & Exception Management)
After planning has set the first steps in planning manually with Anaplan and adopted a new way of working, what could be the next step? Due to the powerful calculation engine of Anaplan, it can perform real-time calculations on very large datasets. This advantage can be used to set up business-specific heuristics to further automate calculations of planning problems, such as calculating order proposals based on a chosen inventory policy, automatic truck/container filling to achieve FTL, etc. Because Anaplan is doing the heavy lifting, in this stage the organization can start shifting to an exception-based way of working and create focus on the most important, value-adding work.
Another possibility to explore at this stage is the creation of scenarios. In Anaplan you are able to save scenarios with different inputs and settings, and calculate in real-time what the outcome of those scenarios is. An example of the use of scenarios in supply chain is for risk and opportunities in demand planning. In Anaplan it is very easy to create new risks or opportunities and simulate the effect on the predicted volumes and turnover.
Run (First Use Case With the Optimizer)
For now, we focused on manual planning, heuristics, and scenarios, which are good starting points. The main advantage of adopting a heuristic approach is that it offers a quick solution, which is easy to understand and implement. However, the main downside of the heuristic approach is that it is, in the vast majority of cases, unable to deliver an optimal solution to a planning and scheduling problem. Additionally, in general, they are harder to combine with the scenario capabilities.
Therefore, once a good planning process is in place and the trust of the planners is gained in Anaplan as a reliable planning tool, we can go for the next step: the first use case of a mathematical optimizer.
Typically there are a couple of disadvantages to using an optimizer in a business context. First, to use optimization models, specific expertise and technologies are required to set them up and use them. Second, you need a thorough understanding of mathematical programming concepts and the utilization of special solvers. With Anaplan these disadvantages are tackled due to how the optimizer functionality of Anaplan works. Setting up the optimization model is done completely in the user-friendly and code-free interface of Anaplan. And thus, technically setting up the optimizer is not more difficult than building any other functionality in Anaplan. For the calculations, Anaplan uses the GUROBI engine, which is a state-of-the-art solver.
Because of this golden combination, the optimizer is not just a black box that no one understands how works. It is easy to identify what variables, constraints, and parameters the model takes into account. This helps in adopting the Anaplan optimizer into your organization.
When exploring the possibility to use the optimizer in a supply-chain context, it is advised to stick to the credo: “start small, scale fast.” Start with a smaller use case, and build on this step by step, taking into account all the learnings during the process.
Fly ( E2E Supply Chain Optimization With Scenarios)
Looking back at the complex environment supply chain is working in and the growing need for agility and fast decision making, we have identified and build in the previous stages' knowledge on key enablers in Anaplan to achieve the final stage of supply chain optimization. The true power of Anaplan for agile E2E supply chain optimization is the combination of the optimizer with the scenario capabilities.
As the optimizer can calculate the optimal solution from a holistic E2E point of view all at once for different scenarios, it is capable of taking into account changing costs (production, inventory, transportation, etc.), changing inputs, and changing constraints (what is the optimal plan if we suddenly cannot ship from DC A to Customer B?) per scenario. Users can save and compare the calculated solutions for the different scenarios, ultimately leading to a decision on the best way forward given the current supply chain context.
If you are at the beginning of your supply chain optimization journey or looking into E2E optimization, bluecrux and Anaplan can support you in this journey.