Optimizing Warehouse Space Utilization
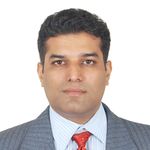
With the unprecedented events of this year, warehouse space utilization planning becomes a key decision-making point to balance supply and demand. Inappropriate warehouse space planning may lead to safety concerns like accidents, higher vehicle turnaround times, demurrages, and product quality that can affect the overall warehouse’s operational efficiency and cost.
Benefits of warehouse space planning include:
- Visibility on future space utilization and planning.
- Reduction in cost due to demurrages, handling damages.
- Improved warehouse safety compliance because of proper space planning.
A common challenge for demand planners, buyers, marketing, and sales teams is that they lack visibility on warehouse space utilization to perform their respective tasks or execute decisions made in day-to-day business with a high degree of certainty. Similarly, for a warehouse manager, it is very difficult to forecast warehouse space utilization accurately at a detailed, granular level considering misaligned estimates provided across different functions.
Warehouse managers are responsible for anticipating and quantifying space utilization related concerns and understanding the risks to enable leadership teams to take appropriate and proactive business decisions at the right time, such as partnering with third-party logistics partners, promotions planning, or order postponement.
Considering typical constraints related to warehouse space planning, there are platforms that can help businesses to integrate different business functions with warehouse planning. Anaplan is a leading global planning platform that caters to continuously Connected Planning, specifically empowering warehouse managers to quickly create and analyze various ‘what if’ scenarios. The ability for business managers to create on-the-fly plan variations during sales and operations meetings to conclude a ‘best fit scenario’ facilitates a more interactive and collaborative approach to streamline the integrated business planning process.
The beauty of using the Anaplan platform is all stakeholders—for instance, demand planners, buyers, or the marketing team—can visualize the impact of their independent decisions against warehouse space utilization without being dependent on a warehouse manager. For example, marketing can create their own ‘what if scenario’ versions and immediately determine the impact on warehouse space against a promotional uplift % applied on top of the baseline.
Anaplan provides flexibility for planning at the most granular levels like ‘Product-Location-Period,’ but it also gives users the capability to automate consolidated warehouse space level planning.
More About Connected Planning:
- Scale with Anaplan: The 3 Tenets of Planning at Scale
- Kick Off Summer by Improving Your Consolidations Process
- Using Data and Technology to Create Value in Your Organization
A warehouse space utilization application built on the Anaplan platform can provide a unique opportunity for a business to connect and synchronize its demand planning function with the warehouse planning function at the most granular level of detail leading to lower cost and better performance. What best practices do your team implement for warehouse space utilization? Share in the comments below.
Amit Chavan is a Certified Master Anaplanner and an Anaplan architect with deep expertise in Supply Chain and S&OP. He has great experience and knowledge in the Supply Chain and has been leveraging Anaplan as the planning platform since his first deployment a few years back.
Comments
-
Great article! You're the expert on supply chain solutions - how well would a warehouse utilisation model compliment your Inventory Optimisation app? https://www.tridant.com/tridant-inventory-optimisation-application
0 -
Thank you!
Well, connecting warehouse space utilization model with Inventory optimization app. can create a very good value to the business.
0